Why Implementing RDS-PP Standards Lowers Wind Turbine Operations and Maintenance Cost
23 April, 2020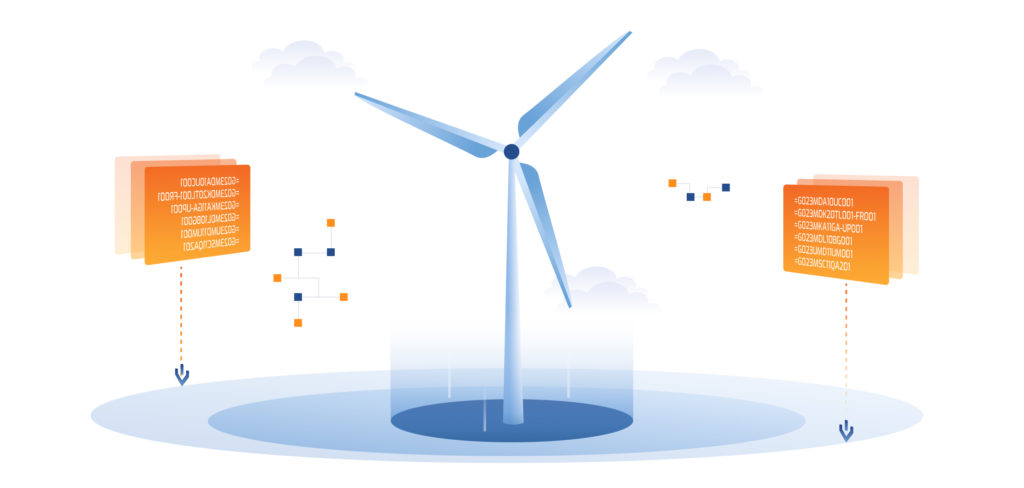
RDS-PP is the preferred system for wind energy, but a lot of wind turbine operators aren’t using it yet. As wind is a relatively new source of energy, wind turbine assets are often mapped according to older standards designed for more traditional energy sources.
However, the wind energy market is expanding. According to the WWEA, the overall capacity of wind turbines worldwide reached 597 Gigawatts in 2018. The United States is the second fastest growing market for wind energy behind China. Wind power capacity in the United States has doubled since 2010, especially in the state of Texas, which supports around 26 percent of the nation’s wind energy at over 25 GW of wind generation capacity.
To keep up with demand, wind turbines have been increasing in size as well as number. In 2018, the average capacity of large-scale wind turbines installed in distributed applications in the United States was 2.1 MW, which is nearly double the capacity of turbines in 2003. Increasingly, more wind turbine farms are also being built offshore, where favorable conditions achieve a capacity factor of 60 percent, 20 percent higher than inland windfarms under favorable conditions. However, offshore windfarms are more expensive to operate and maintain. In addition to being more difficult to get to, offshore wind turbines have subsea foundation structures that must be monitored and repaired in addition to the wind turbines themselves.
Importance of wind turbine components classification
The data generated by wind turbines is essential to identifying and repairing component failures before they can create damage. When turbines aren’t operating correctly, it means less energy is being generated, which means lost revenue.
When planning for the construction of new wind farms or servicing equipment in remote, difficult-to-reach locations or out at sea, you don’t want engineers and operators guessing about how things are organized, the problems that need to be fixed, or the parts that need to be ordered or replaced.
To avoid this, each component needs to be mapped according to an identification and classification system that creates a common language for reference between parties. There are technically two international standards that are widely popular—the KKS and the RDS-PP. The KKS Identification System for Power Plants has been used successfully worldwide since the 1970s, but it is the older standard today. RDS-PP is the successor of KKS. It stands for Reference Designation System for Power Plants and is based on structuring principles, designation rules and letter codes specified in international standards (ISO) for the designation of technical objects within a system. The KKS system is fine for energy companies that have already invested in it or must use it for consistency because their suppliers do, but the RDS-PP is a newer, better standard.
Common practices
Many organizations don’t use an international standard at all. Many create their own system of hierarchy for the production aspects of wind turbines (how the wind turbines are manufactured), as well as the location, system structure, and function of each asset. These are usually mapped inside an ERP according to asset function, equipment and materials. Function is usually mapped to the main asset level – sometimes called an aggregated asset in SAP. The next asset level is the equipment level. The lowest asset level encompasses all the maintainable parts, which is what allows for corrective and preventative maintenance of wind turbine equipment. However, this lowest maintainable level often doesn’t get properly mapped, resulting in unidentified assets and structural inconsistencies that can affect the entire fleet.
This function, equipment, materials approach to hierarchy can lead to a host of other problems. For example, there will inevitably be poor maintenance history. In the maintenance and operations of wind turbines, it’s common to move parts around between assets to optimize operational efficiency. Without reliable data at the individual parts level, historical maintenance data will disappear from one main asset when related equipment is transferred to another asset. This also impacts the ability to benchmark between farms, areas, and designs. The result is increased maintenance and inventory costs.
Why implement RDS-PP?
RDS-PP is superior because it is more thorough and more universal. With RDS-PP, operators and engineers can interpret a string of code to identify the power plant, the section of the power plant, the type of power plant, the equipment in question and every individual component in need of attention or service. This identification system is structured according to hierarchy with clear and consistent definitions that – once understood – is easy to read by all parties involved in the lifecycle of a wind turbine. For example, G001 MDL10 MZ010-MA001 would be understood by all involved parties as motor 1 of the first wind turbine’s yaw drive 1.
With RDS-PP, it is possible to streamline everything from identifying performance issues to ordering replacement parts. Implementing the RDS-PP standard is also helpful in planning the development of new wind farms and expanding the total number of wind turbines. When combined with asset management software and real-time data analytics available from SAP ERP, wind energy companies can enjoy increased ease of integrations, risk mitigation, condition monitoring, and accuracy during inspection and repairs.
With implementation of the RDS-PP standard for operational wind turbines, the time required to replace broken parts improves by as much as 500 percent. This is because technicians can use the detailed hierarchy system to correctly identify the correct part from a list of parts mapped to the wind turbine’s function. The technician does not have guess which part is needed by looking at pictures of the part or trying to identify it by the nameplate. In addition, the visits to wind turbines tend to decrease by as much as 50 percent per year. When the data is mapped in an ERP system according to the RDS-PP international standard, an alert is triggered automatically upon failure, negating the necessity for site visits just to check that all components are operational. When there is a failure, the technician doesn’t have to make a trip to the location to identify which part is the issue. They also don’t have to make additional trips to correct issues that were misidentified. This information is all available in the software.
In other words, by combining analytics with an internationally standardized system for labeling assets like RDS-PP, wind turbine components can be monitored from a distance and repaired proactively. With the RDS-PP, individually labeled data points with definitive reference addresses act as engineering databases for plant management software. Properly applied, turbines provide real-time data on each of their own components. Management and repair of failed components becomes a lot easier when information is labeled and categorized using the same code to identify and prevent potential problems and share information across suppliers and operators.
RDS-PP is of particularly high value to enterprise-level energy companies who manage wind energy assets in incredibly large numbers. In the United States, for example, the U.S. Wind Turbine Database (USWTDB) contains more than 58,000 turbines. The data generated by wind turbines makes communication on the operations and maintenance of wind farms more efficient. Wind turbines also provide data that is useful for land and resource management, including data on the weather and wind speeds. Ultimately, the operational data collected helps an energy company to compare and contrast the efficiency and reliability of different wind energy plants and optimize performance across the portfolio.
Keel RDS-PP implementation services and experience
Keel Solution specializes in wind energy and has years of experience implementing RDS-PP standards and mapping the data in SAP ESP for large enterprise-level energy companies. RDS-PP for the wind industry is not self-explanatory. It needs to be learned like any other language, and the RDP-PP language is young and evolving. The documentation available on the RDS-PP standard for wind turbines is a good overview, but an experienced specialist is needed to solve for gaps and unclear boundaries in manner consistent with best practices. There are third party groups working on closing the gaps and clarifying the boundaries with RDS-PP (Keel Solution is a partner with one of these groups), but most companies looking to implement RDS-PP will still benefit from consulting.
It is common for energy companies to attempt to implement RDS-PP as a one-off project solution for a new wind turbine farm or maintenance project without looking at the needs of the legacy fleet.
Keel Solution has years of experience managing successful implementations of the RDS-PP standard for different wind turbine types, substations, and manufacturers and can advise on the best approach.
Services include asset data cleansing, data migration, data mergers, and development of a reference for RDS-PP structure tailored to the need of the individual customer. Resources include asset data management engineers, SAP specialists, and technical engineers with over a decade of experience working together on implementations of industrial energy standards, four of which are specifically in the wind energy industry.
If you are interested in implementing RDS-PP standards for wind energy or already utilize RDS-PP but need to integrate and align the data with your asset management software, contact us for a consultation on how we can help.
RDS-PP and ERP Service Specification
Read more about our RDS-PP services:
- Maximize Efficiency with our ISO 14224 services
- Unlocking the Power of Data Governance: Overcoming Challenges and Maximizing Potential
- Unleashing Efficiency: A Cutting-Edge Approach to Offshore Drilling Rig Maintenance
- RDS-PP Implementation – Are you lost in transition?
- RDS-PP implementation statistics
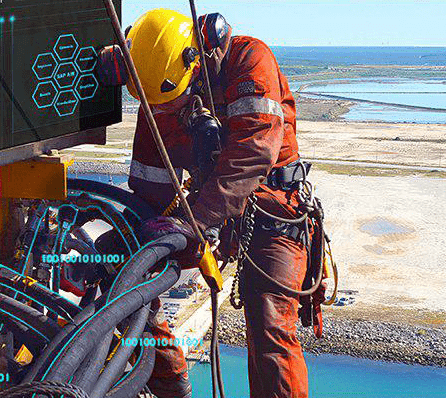
Oil and Gas Asset Data Management
Harness the technology advancements and incorporate the Industry 4.0 into your Oil&Gas business
More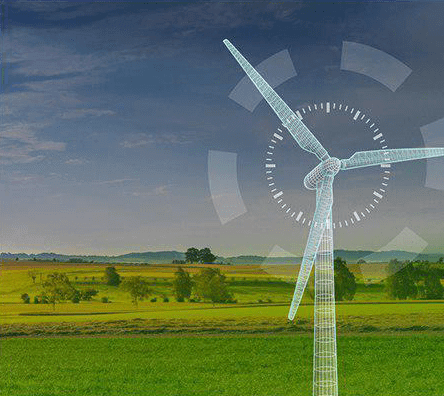
Windpower Competency Center
Opening the door of Industry 4.0 possibilities
MoreWe are ready to help!
Request consultation, ask a question or share your feedback. Just get in touch!