Saving Money by Resolving 4 Small Problems in the Warehouse
31 May, 2021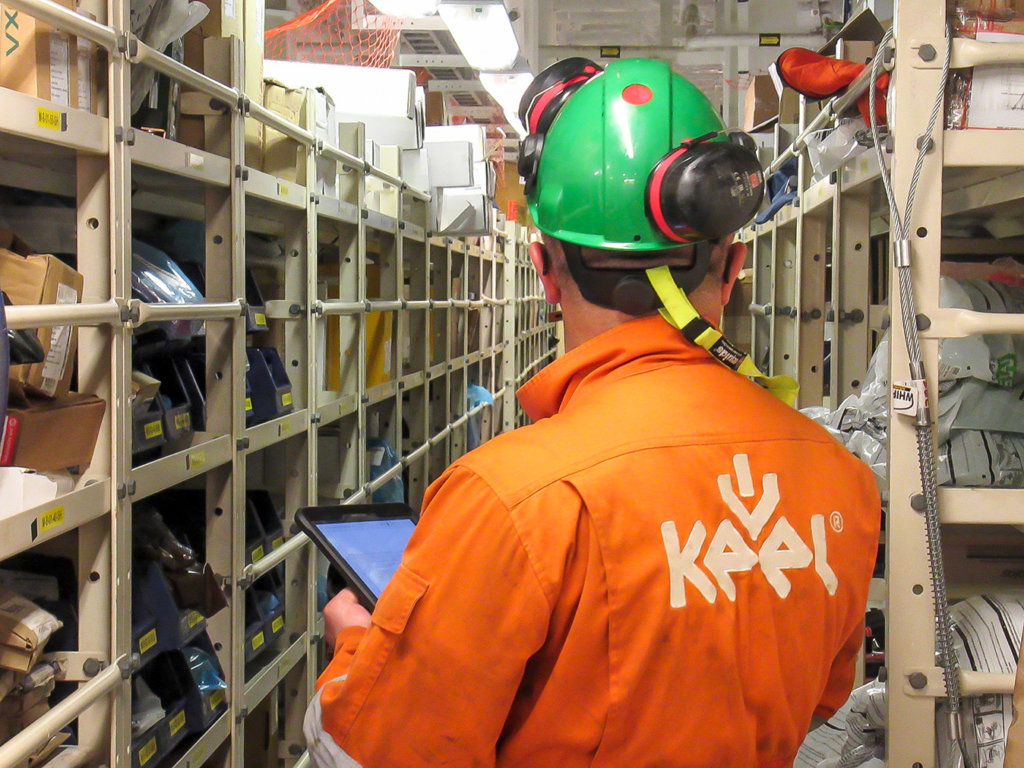
By Vasyl Panasiuk, Senior Engineer
Problem 1: Housekeeping
In today’s warehouse management, the only thing that matters is the presence of a material, not its location. However, disorder, heaping, dirt, dust, lack of light and labeling can all lead to a lot of time spent searching for and issuing materials.
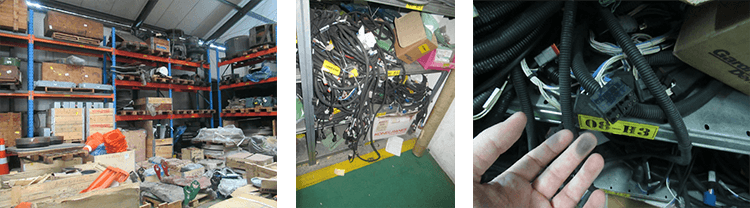
SOLUTION:
Сleaning:
The warehouse must be well-groomed with proper shelving and enough space to move parts.
Ensure that the space has adequate lighting and take the necessary measures to prevent dirt and dust:
- Use and clean filters in the ventilation system
- Implement wet floor cleaning on a daily or weekly basis
- Ensure hermetic packaging of materials
- Keep the working floor clear
Sorting:
To reduce time spent locating an item, decrease the number of items and sort them by:
- Equipment / unit where they are used
- Type (electric, hydraulic, etc.)
- Material (rubber, liquids, aerosols)
- Hazard class (toxic, flammable, explosive)
- Weight – heavy spare parts should be kept on the ground and small inventory should have a bin system
Inactive spares should be kept outside of the main warehouse or in a separate place, and unnecessary items should be removed. It is a good idea to increase the amount of available useful space and improve safety by eliminating obstacles.
Orderliness
- Racks and shelves must have a clear and easy to understand numbering system; this will ensure that all the necessary items are put in the optimal place, making them easily found later.
- Make sure the workflow is smooth and efficient.
- Arrange all necessary items so that they can be easily selected for use.
- Assign fixed locations for items; do so by using clear labels, marks or hints; this will make the items easy to return to their correct locations. It will also be easy to spot missing items.
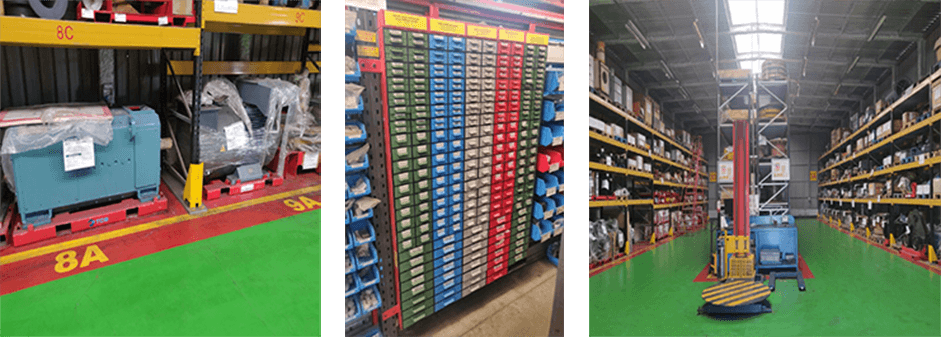
Problem 2: Packaging
Insufficient quantity or an absence of packaging materials (foam drops, stretch film, different sizes of plastic bags, etc.) leads to materials losing their quality, thereby making them unsuitable for future use and resulting in loss of money.
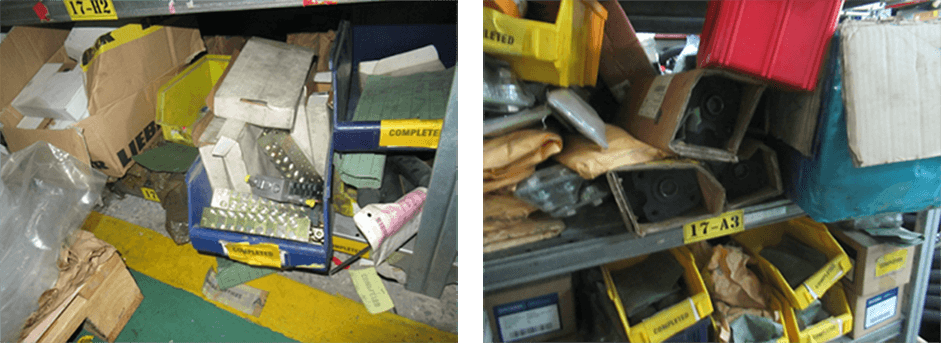
SOLUTION:
All storage materials should be packed in such a way so as to prevent dust, moisture, and excessive dryness. To do so, you need to use:
- Foam drops
- Stretch film
- Plastic bags
- Grease
- Paper boxes
Small size materials should be placed in colored bins or paper boxes. Packaged materials must have a label with a description that includes:
- Local part number
- Description of the material
- Manufacturer name and part number
- Location number on rack
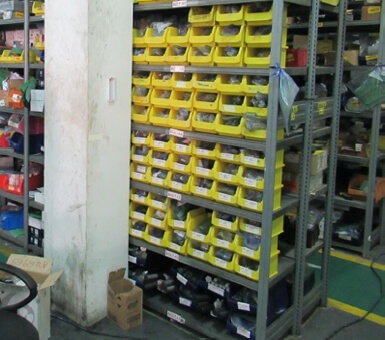
Packaged materials will have a longer shelf-life, which will save money.
Problem 3: Obsolete materials
Obsolete inventory is a term that refers to inventory at the end of its product life cycle. This inventory has not been used for a long period of time and is not expected to be used in the future. This type of inventory has to be written off and can cause significant financial loss for a company.
Obsolete materials in the warehouse are usually the result of an excessive initial purchase order and/or not tracking the expiration date. Further, old unused materials end up being thrown away in favor of using the newly bought ones.
Unfortunately, such materials can accumulate in huge amounts over several years, and their price can soar to hundreds of thousands of dollars.
SOLUTION:
In order to reduce and/or prevent the occurrence of obsolete materials, it is important to understand the need behind keeping track of these materials.
Inventory, by definition, is demand within lead time. Therefore, decisions to stock inventory (parts owned and located in an onsite warehouse) are made to mitigate delays during lead times, given the probability of unplanned demand requirements. Most modern EPRs run basic replenishment MRP (Materials Resource Planning) type functionality, so parts ordering can be automated.
There are many ways to calculate safety stock and reorder periods; this calculation depends on the type of demand (lumpy, smooth, periodic, seasonal, or other). For example, transactional consumption history may require a greater use of formulas that use inventory classification. For lumpy or very low consumption history, it might be best to conduct a manual review using criticality assessments and risk matrices. Unfortunately, in high-asset equipment environments, there is a second category which requires the majority of inventory to be classified using personal experience and biases in an appropriate internal framework.
Problem 4: Improper storage of hazardous materials
One of the typical problems we encounter in warehouses is improper storage of hazardous materials. This is usually a result of a lack of experience in the basic requirements for storing hazardous materials, lack of training, and sometimes simply just from ignorance of these rules.
From our experience, staff who work with the same daily routine for a long time can often overlook many things and are not able to evaluate everything with a fresh set of eyes. Unfortunately, they often do not even notice violations that have been repeated for many years; worst of all, they might not be ready to change it. During training, raising awareness and providing adequate instruction is vital to preventing these scenarios.
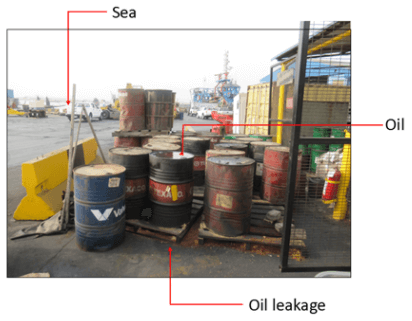
SOLUTION:
- Organize regular trainings to determine hazard class of materials
- Identify storage areas for hazardous materials
- Provide personal protective equipment for staff
- Comply with fire safety rules
- Organize trainings on disposal of hazardous substances
Substances and materials can pose the potential danger of causing a fire, exacerbating fire hazards, poisoning the environment (air, water, soil, flora and fauna, etc.), and affecting humans through the skin (either via mucous membranes of the respiratory organs by direct action or at a distance). They can be divided into into four risk level categories:
- safe
- low-hazardous
- dangerous
- especially dangerous
The conditions of their storage are determined by the category of the substances and materials.
- Safe: non-combustible substances and materials in non-combustible packaging, which in case of fire do not emit hazardous (flammable, poisonous, or corrosive) decomposition or oxidation products. They also do not form explosive or flammable, toxic, corrosive, exothermic mixtures with other substances. Safe substances and materials are stored indoors or on sites of any type.
- Low-hazardous: combustible and flame-retardant substances and materials, as well as non-combustible substances and materials in combustible packaging.
- Dangerous: combustible and non-combustible substances and materials that have properties which can lead to explosion, fire, death, injury, poisoning, radiation, human and animal diseases, as well as damage to buildings and vehicles.
- Particularly dangerous: substances and materials that are not compatible with substances and materials of the same category. They must be stored in warehouses of first and second level of fire resistance located mainly in individual buildings.
Contact us for a consultation on how we can help you optimize your warehouse management.
- SAP Classification: Structure & Enrich Master Data for Business Results
- Maximize Efficiency with our ISO 14224 services
- Unlocking the Power of Data Governance: Overcoming Challenges and Maximizing Potential
- Unleashing Efficiency: A Cutting-Edge Approach to Offshore Drilling Rig Maintenance
- RDS-PP Implementation – Are you lost in transition?
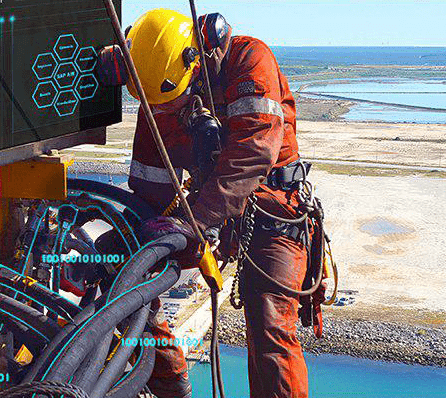
Oil and Gas Asset Data Management
Harness the technology advancements and incorporate the Industry 4.0 into your Oil&Gas business
More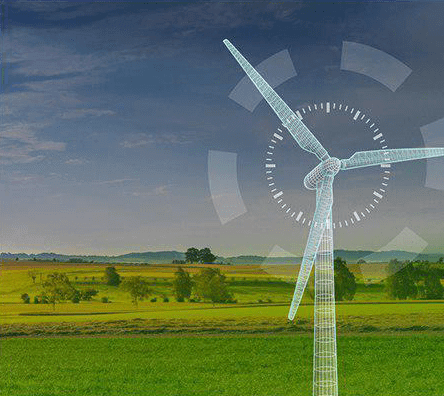
Windpower Competency Center
Opening the door of Industry 4.0 possibilities
MoreWe are ready to help!
Request consultation, ask a question or share your feedback. Just get in touch!